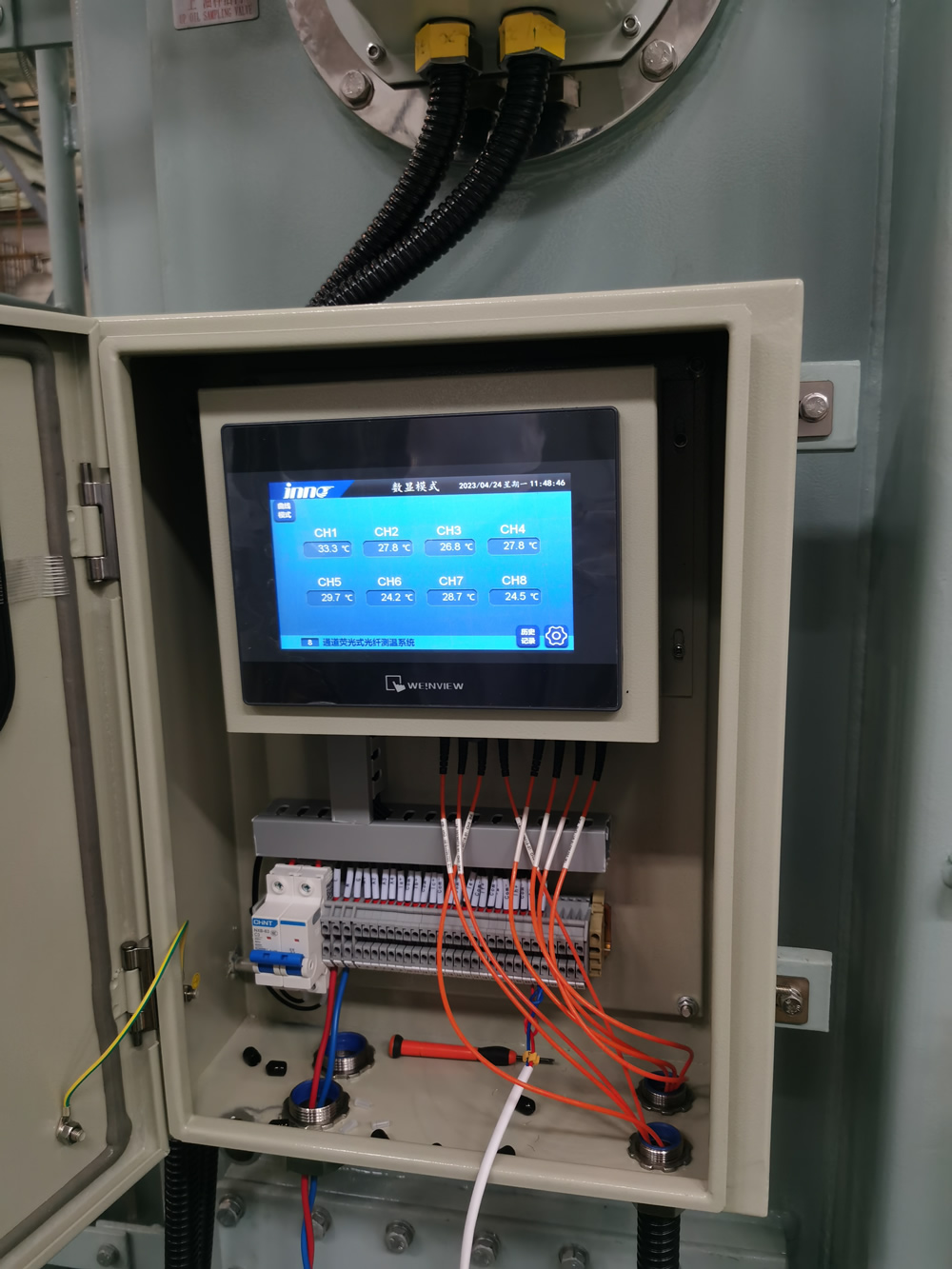
Sa ki nan liv sa ki sou li yo
- Introduction: The Critical Role of Temperature Monitoring in Transformer Performance
- Fiber Optic Temperature Sensing Technology: How It Works
- Key Advantages of Fiber Optic Temperature Sensors for Transformer Applications
- Comparing Fiber Optic Technologies: DTS vs. FBG vs. Fluoroptic Systems
- Gid aplikasyon: Where and How to Install Fiber Optic Sensors in Transformers
- Real-World Case Studies: Transformer Failure Prevention
- ROI Analysis: The Business Case for Fiber Optic Temperature Monitoring
- Selection Guide: How to Choose the Right Fiber Optic System for Your Transformers
- Future Trends: The Evolution of Fiber Optic Monitoring in 2025 and Beyond
- Conclusion: Implementing a Fiber Optic Temperature Monitoring Strategy
Introduction: The Critical Role of Temperature Monitoring in Transformer Performance
Power transformers represent some of the most critical and expensive assets in the electrical grid. With replacement costs ranging from hundreds of thousands to millions of dollars and lead times often exceeding 12 Mwa, unexpected transformer failures can have devastating impacts on grid reliability, operational costs, and organizational reputation.
At the heart of transformer reliability lies temperature management. As IEEE and IEC standards have long established, elevated operating temperatures are directly correlated with accelerated insulation aging, with each 7-8°C increase potentially halving the expected transformer life. While traditional oil and winding temperature indicators have served the industry for decades, they provide only limited insight into actual conditions within the transformer.
of transformer failures are related to excessive temperatures or hotspots
typical difference between average winding temperature and actual hotspot temperature
reduction in transformer life for every 7-8°C increase in operating temperature
months typical lead time for critical power transformer replacement
Fiber optic temperature sensing technology has revolutionized the approach to transformer temperature monitoring, providing direct, real-time measurement of actual winding hotspot temperatures rather than approximations based on oil temperatures and thermal models. As we move further into 2025, these systems have become increasingly sophisticated, offering unprecedented insight into transformer thermal behavior and enabling truly condition-based maintenance approaches.
This comprehensive guide explores the latest developments in fiber optic temperature sensing for power transformers, from the fundamental technology principles to practical implementation strategies, helping asset managers, electrical engineers, and maintenance professionals make informed decisions about this critical monitoring technology.
Fiber Optic Temperature Sensing Technology: How It Works
Fiber optic temperature sensing represents a fundamental departure from conventional electrical temperature measurement techniques. Instead of relying on electrical signals that can be compromised by electromagnetic interference (EMI), fiber optic sensors use light properties to detect temperature changes with exceptional accuracy and reliability.
Core Technology Principles
Fiber optic sensors operate based on several different physical principles, each with specific advantages for particular applications:
Fluorescence Decay Method (FDM)
This method utilizes temperature-sensitive phosphorescent materials at the sensor tip. When excited by a light pulse, these materials emit fluorescent light with decay characteristics directly related to temperature. The time-based measurement is inherently immune to light intensity fluctuations, making it exceptionally accurate and stable over long periods.
Typical accuracy: ±0.5 °C
Fib Bragg Grating (FBG)
FBG sensors contain microscopic periodic variations in the refractive index of the fiber core, creating a wavelength-specific reflector. As temperature changes, thermal expansion alters the grating period, shifting the reflected wavelength proportionally to temperature. This allows for multiplexing multiple sensors on a single fiber.
Typical accuracy: ±1.0 °C
Distribye Sans tanperati (DTS)
DTS systems measure temperature continuously along the entire length of an optical fiber. They work by analyzing the backscattered light resulting from the Raman effect. The ratio between Stokes and anti-Stokes signals provides temperature information, while the time-of-flight determines the location along the fiber.
Typical accuracy: ±1.0-2.0°C with spatial resolution of 1-2 meters
Typical System Components
A complete fiber optic temperature monitoring system for transformers typically includes:
Fiber Optic Probes
Specially designed temperature probes containing optical fibers that are installed directly into transformer windings during manufacturing or retrofit procedures. These probes are engineered to withstand the harsh electrical, thermal, and chemical environment inside transformers for decades.
Signal Conditioner/Transmitter
Electronic equipment that generates the light signals, analyzes the returned optical signals, and converts them into temperature readings. Modern units provide multiple communication interfaces including 4-20mA, Modbus, DNP3, and IEC 61850 for seamless integration with SCADA and asset management systems.
Extension Fibers
Specialized optical fiber cables connecting the probes to the signal conditioner, designed to withstand the transformer oil environment and provide reliable transmission over long distances without signal degradation.
Monitoring Software
Advanced software platforms that display real-time temperature data, analyze trends, generate alerts, and integrate with broader asset performance management systems to enable condition-based maintenance strategies.
Transformer Installation Approaches
Fiber optic temperature sensors can be integrated into power transformers through several methods:
Factory Installation (New Transformers)
The optimal approach involves installing sensors during transformer manufacturing, allowing precise placement at calculated hotspot locations within the windings. Sensors are typically integrated into specialized spacers or directly between disc windings.
Retrofit Installation (Existing Transformers)
For transformers already in service, special retrofit probes can be installed through available openings such as unused thermometer wells, spare valves, or inspection ports. While not providing the same level of direct winding access as factory installation, these approaches still deliver valuable temperature data.
External Surface Monitoring
For applications where internal access is impossible, advanced DTS systems can be installed on transformer tank surfaces to provide thermal mapping of external temperatures, which can be correlated to internal conditions through sophisticated thermal modeling.
Technology Evolution: 2025 Update
Recent advances in fiber optic sensing technology have dramatically improved system performance. The latest generation of monitoring systems now offers:
- Enhanced accuracy (±0.2°C in laboratory conditions, ±0.5°C in field applications)
- Expanded measurement range (-40° C +300 ° C)
- Increased sampling rates up to 10Hz for dynamic load studies
- Advanced self-calibration capabilities ensuring drift-free operation over decades
- Miniaturized probes with diameters as small as 0.8mm for minimal impact on transformer design
- Built-in redundancy with dual optical paths for mission-critical applications
Key Advantages of Fiber Optic Temperature Sensors for Transformer Applications
The adoption of fiber optic temperature monitoring technologies for power transformers has accelerated significantly in recent years, driven by several compelling advantages over conventional monitoring approaches. Understanding these benefits is essential for asset managers and engineers evaluating monitoring system investments.
Direct Hotspot Measurement
Conventional approach: Traditional winding temperature indicators (WTIs) estimate hotspot temperatures based on top oil temperature plus a thermal model offset that approximates winding temperature rise.
Fiber optic advantage: Sensors directly measure actual winding temperatures at the predicted hotspot locations, eliminating estimation errors that can exceed 15°C during transient conditions or unusual loading patterns.
Impact: Accurate hotspot data enables precise loading decisions, preventing unnecessary derating while avoiding dangerous overloading conditions.
Immunity to Electromagnetic Interference
Conventional approach: Electrical sensors like RTDs and thermocouples can suffer from measurement errors, signal degradation, or outright failure due to the intense electromagnetic fields present in transformers.
Fiber optic advantage: The dielectric nature of optical fibers makes them completely immune to EMI, ensuring reliable measurements even during fault conditions, switching operations, or geomagnetic disturbances.
Impact: Continuous, reliable data during all operational states, including critical fault conditions when temperature information is most valuable.
Multiple Measurement Points
Conventional approach: Traditional systems typically provide only 1-2 temperature measurement points per transformer due to cost and complexity limitations.
Fiber optic advantage: Modern systems support 8-16 discrete measurement points in a single transformer, enabling comprehensive thermal mapping of different winding sections, phases, and core components.
Impact: Detailed thermal profiles reveal unexpected temperature distributions, design issues, or cooling problems that would remain hidden with limited measurement points.
Enhanced Safety and Isolation
Conventional approach: Electrical sensors require careful isolation design to prevent dangerous potential transfer between windings and monitoring equipment.
Fiber optic advantage: The inherent electrical isolation of optical fibers eliminates any risk of potential transfer, ground loops, or safety hazards, simplifying installation and improving personnel safety.
Impact: Reduced engineering complexity, elimination of isolation barriers, and enhanced safety for maintenance personnel.
Long-Term Stability
Conventional approach: Electrical sensors typically experience calibration drift over time, particularly in high-temperature environments with thermal cycling.
Fiber optic advantage: Premium fiber optic systems utilize reference-based measurement principles that are inherently stable, with documented cases of sensors maintaining calibration for 25+ years in transformer applications.
Impact: Virtually elimination of recalibration requirements, reducing maintenance costs and ensuring reliable data throughout the transformer lifecycle.
Dynamic Load Management
Conventional approach: Conservative loading based on nameplate ratings or simplified thermal models, often leaving significant capacity unutilized.
Fiber optic advantage: Real-time hotspot measurement enables dynamic loading beyond nameplate ratings when conditions permit, while maintaining safe thermal limits.
Impact: Studies show capacity increases of 10-30% are often possible without exceeding design temperature limits, significantly enhancing asset utilization.
Cooling System Effectiveness Verification
Conventional approach: Limited ability to verify actual cooling system performance or detect partial cooling failures.
Fiber optic advantage: Multiple temperature sensors provide clear thermal signatures of cooling system effectiveness, instantly revealing plugged radiators, fan failures, or pump issues.
Impact: Early detection of cooling problems before they impact transformer life or trigger alarms, enabling proactive maintenance.
Advanced Analytics Integration
Conventional approach: Limited temperature data restricts the effectiveness of asset health analytics.
Fiber optic advantage: Rich, multi-point temperature datasets enable sophisticated analysis including thermal modeling, remaining life estimation, and anomaly detection algorithms.
Impact: Enhanced predictive maintenance capabilities, better capital planning, and reduced risk of unexpected failures.
Real-World Example: Capacity Release in Transmission Transformer
A major North American utility installed fiber optic temperature monitoring in a critical 500MVA transmission transformer previously limited to 85% loading due to conservative temperature estimates. Direct hotspot monitoring revealed actual temperatures were 12°C lower than calculated values during peak loading conditions. This enabled an immediate 15% increase in allowable loading, deferring a $5.2M capacity upgrade project by 4 years while maintaining full compliance with IEEE thermal guidelines.
Comparing Fiber Optic Technologies: DTS vs. FBG vs. Fluoroptic Systems
The fiber optic temperature sensing market offers several distinct technologies, each with unique characteristics that make them suitable for different transformer monitoring applications. Understanding these differences is crucial for selecting the optimal solution for specific needs.
Characteristic | Fluoroptic Systems | Fib Bragg Grating (FBG) | Distribye Sans tanperati (DTS) |
---|---|---|---|
Measurement Principle | Phosphorescent decay time measurement | Wavelength shift of reflected light | Raman backscatter intensity ratio |
Typical Accuracy | ±0.2°C to ±0.5°C | ±0.5°C to ±1.0°C | ±1.0°C to ±2.0°C |
Rezolisyon espasyal | Point measurements only | Point measurements (multiple per fiber) | Continuous (typically 1m resolution) |
Maximum Points per System | 8-16 channels typical | 20-80 sensors per fiber | Thousands of measurement points |
Measurement Speed | Fast (multiple readings per second) | Moderate (1-10 seconds for full scan) | Slower (30 seconds to several minutes) |
Probe Durability | Excellent for transformer environments | Good, but requires strain management | Excellent with proper cable selection |
System Cost Range | $15,000-$40,000 (8 chanèl yo) | $30,000-$60,000 (16-32 Pwen) | $50,000-$100,000+ (full system) |
Integration Complexity | Simple point-to-point architecture | Moderate complexity | Higher complexity, specialized software |
Ideal Applications | Direct winding hotspot monitoring | Multi-point monitoring with strain/vibration | Surface mapping, bushings, leads, tanks |
Fluoroptic Technology Deep Dive
Fluoroptic technology (also called fluorescence decay method) has become the dominant approach for transformer winding hotspot monitoring due to its exceptional accuracy, stability, and simplicity. These systems use a phosphorescent material at the sensor tip that, when excited by a light pulse, emits a fluorescent signal with decay characteristics directly proportional to temperature.
The time-based measurement approach makes these systems inherently immune to light intensity variations, fiber bending losses, or connector degradation. Leading manufacturers like Neoptix (acquired by Qualitrol) and Rugged Monitoring have refined this technology specifically for transformer applications.
Key advantages for transformer applications include:
- Highest accuracy (±0.2°C in controlled conditions)
- Exceptional long-term stability without recalibration
- Simple, robust probes that withstand transformer environments
- Fast response times for dynamic loading studies
- Compatibility with both new transformer installations and retrofits
FBG Technology Deep Dive
Fiber Bragg Grating technology utilizes microscopic modifications to the fiber core that create wavelength-specific reflectors. As temperature changes, these gratings expand or contract, shifting the reflected wavelength proportionally.
The key advantage of FBG systems is multiplexing capability, allowing dozens of discrete sensors on a single fiber. Some advanced systems combine temperature and vibration/strain measurement in the same fiber, providing multidimensional condition monitoring.
Key advantages for transformer applications include:
- Multiple measurements on a single fiber (reduced installation complexity)
- Combined temperature and vibration monitoring capabilities
- Good accuracy suitable for most applications
- Excellent EMI immunity and long-distance capabilities
- Lower per-point cost in large multi-sensor deployments
DTS Technology Deep Dive
Distributed Temperature Sensing provides continuous temperature measurement along the entire length of an optical fiber, rather than at discrete points. These systems operate based on the Raman scattering principle, where backscattered light includes temperature-dependent components.
By analyzing the ratio of Stokes to anti-Stokes signals and using time-domain reflectometry to determine position, DTS systems create complete temperature profiles. While traditionally used for longer distances in pipeline or cable monitoring, specialized high-resolution DTS systems have emerged for transformer applications.
Key advantages for transformer applications include:
- Complete surface temperature mapping without sensor placement planning
- Ability to detect unexpected hotspots anywhere along the fiber path
- Excellent for bushing monitoring, lead connections, and tank surfaces
- Single fiber installation for hundreds or thousands of measurement points
- Visualization capabilities for thermal mapping of entire transformers
Technology Selection Guidance
When selecting fiber optic temperature monitoring technology for transformer applications, consider these application-specific recommendations:
For Critical Power Transformers (>100MVA)
Recommended technology: Fluoroptic point sensors for direct winding hotspot monitoring, potentially combined with DTS for surface/bushing monitoring.
Rationale: The highest accuracy and reliability are paramount for these critical assets, justifying the investment in premium point-sensing technology for direct winding monitoring.
For Distribution Transformers with Limited Access
Recommended technology: DTS systems applied to external surfaces and accessible areas.
Rationale: When direct winding access is unavailable, DTS provides the most comprehensive monitoring solution without requiring internal sensors.
For Transformer Fleet Monitoring Programs
Recommended technology: FBG systems with multiplexed sensors.
Rationale: The cost efficiency of multiplexed FBG sensors makes them attractive for large-scale deployments across multiple transformers, especially when combined with centralized monitoring architecture.
For Research and Development Applications
Recommended technology: Combination of fluoroptic sensors and high-resolution DTS.
Rationale: R&D applications benefit from the high accuracy of fluoroptic sensors at critical locations combined with the comprehensive coverage of DTS systems to discover unexpected thermal behaviors.
Gid aplikasyon: Where and How to Install Fiber Optic Sensors in Transformers
Proper placement and installation of fiber optic temperature sensors is critical to realizing their full potential for transformer monitoring. This section provides detailed guidance on sensor location selection, installation methodologies, and best practices for both new and existing transformers.
Optimal Sensor Placement Strategies
The strategic placement of temperature sensors within a transformer requires balancing theoretical hotspot prediction with practical installation considerations:
Primary Winding Hotspots
For direct winding temperature measurement, sensors should be placed at the theoretical hotspot locations, typically:
- Top third of the winding height (approximately 70-80% from bottom)
- Inner winding layers for disc-type windings
- Near the top oil ducts where oil flow may be restricted
- In areas with highest calculated current density
IEEE thermal models and manufacturer thermal simulations should guide specific placement in each transformer design.
Multiple Winding Coverage
For comprehensive monitoring, sensors should be distributed across different winding structures:
- High-voltage windings (typically 2-4 detèktè)
- Low-voltage windings (typically 2-4 detèktè)
- Tertiary windings (1-2 sensors if present)
- All three phases for three-phase transformers
This distribution enables comparative analysis between windings and phases to identify asymmetrical heating patterns that may indicate developing problems.
Supplementary Monitoring Points
Beyond primary winding measurements, additional strategic locations include:
- Core leg and yoke temperatures
- Main tank oil at different heights
- Cooling system inlet/outlet points
- Lead connections and bushings
- OLTC compartments
These supplementary points create a more complete thermal profile of the transformer system.
Installation Methodologies
Factory Installation (New Transformers)
For new transformers, factory installation during manufacturing provides optimal sensor placement:
- Design Phase Integration: Sensor locations should be specified during the design phase, with thermal modeling determining optimal points.
- Winding Integration: Sensors are typically installed in specialized spacers, between disc windings, or in dedicated sensor channels designed into the winding structure.
- Fiber Routing: Fibers are carefully routed through the winding structure, avoiding sharp bends and potential stress points.
- Terminal Integration: Fibers exit the active part through specially designed sealing systems that maintain oil integrity while protecting the fibers.
- Extension Connection: Extension fibers connect from transformer tank to the monitoring equipment, typically using specialized feedthroughs.
Factory installation requires close coordination with the transformer manufacturer but provides the highest quality and most reliable installation.
Retrofit Installation (Existing Transformers)
For transformers already in service, several retrofit approaches are available:
- Thermometer Well Replacement: Existing thermometer wells can be replaced with specialized fiber optic probes that extend further into the oil, providing more accurate oil temperature measurement.
- Spare Valve Port Installation: Many transformers have spare 1″ or 2″ valves that can be used to insert specialized retrofit probes that extend toward winding structures.
- Inspection Port Access: During planned maintenance that involves opening inspection ports, custom probes can be installed that reach specific internal components.
- External Surface Monitoring: DTS systems can be installed on external tank surfaces, radiators, and cooling equipment without any internal access.
While retrofit installations typically cannot achieve the same level of direct winding access as factory installations, they still provide valuable temperature data that significantly improves upon traditional indicators.
Implementation Best Practices
Fiber Protection and Routing
- Use PTFE or specialized oil-resistant materials for fiber protection within the transformer
- Maintain minimum bend radius (typically >20mm) at all points
- Route fibers to avoid areas with highest electromagnetic fields when possible
- Secure fibers at regular intervals to prevent movement during transportation
- Provide strain relief at all transition points and connections
Connection and Termination
- Use oil-tight feedthroughs specifically designed for fiber optic applications
- Install terminal boxes with sufficient space for fiber service loops
- Label all fibers clearly with permanent identification
- Document exact sensor locations in transformer documentation
- Consider redundant fiber paths for critical measurement points
Monitoring Equipment Installation
- Place monitoring equipment in controlled environments when possible
- Ensure proper power supply with UPS backup for critical applications
- Provide appropriate surge protection for communication interfaces
- Use industrial-grade network equipment for SCADA integration
- Consider cybersecurity requirements for networked equipment
System Commissioning
- Verify all sensor readings before transformer energization
- Compare fiber optic readings with conventional indicators during initial operation
- Document baseline temperature profiles during various loading conditions
- Configure appropriate alarm thresholds based on transformer design limits
- Train operations personnel on system capabilities and limitations
Implementation Checklist
Pre-Implementation Planning
- Define monitoring objectives and critical parameters
- Review transformer design and identify optimal sensor locations
- Select appropriate sensing technology for the application
- Define integration requirements with existing systems
- Establish budget and implementation timeline
System Design
- Specify number and location of temperature sensors
- Determine fiber routing paths and protection requirements
- Select appropriate feedthrough and connection systems
- Design monitoring equipment location and installation
- Plan communication interfaces and protocols
Implementation
- Coordinate installation with manufacturer or maintenance provider
- Document exact sensor locations during installation
- Test all optical connections before finalizing installation
- Verify signal quality and sensor response during testing
- Install and configure monitoring equipment
Commissioning and Operation
- Verify system operation during controlled testing
- Configure alarm thresholds and notification systems
- Integrate data with asset management systems
- Train operations and maintenance personnel
- Establish regular data review procedures
Real-World Case Studies: Transformer Failure Prevention
The true value of fiber optic temperature monitoring becomes evident through real-world applications where these systems have prevented failures, extended transformer life, or enabled enhanced operational capabilities. The following case studies demonstrate the practical benefits across different transformer types and operating environments.
Ka Etid 1: Early Detection of Cooling System Failure in GSU Transformer
Background
A 750MVA generator step-up transformer at a major thermal power plant was equipped with fiber optic temperature sensors in each phase of both primary and secondary windings during manufacture. The transformer had been in service for approximately 3 years when the monitoring system detected an anomaly.
Detection
During routine operation at 85% load, operators noticed an alert from the fiber optic monitoring system indicating an unusual temperature differential between phases. While the C-phase winding temperature was 12°C higher than A and B phases, conventional oil temperature indicators showed normal readings with minimal difference between phases.
Investigation
The detailed temperature data from multiple sensors allowed engineers to identify a specific pattern: temperatures were elevated only in one vertical section of the C-phase winding, suggesting a localized cooling issue rather than an electrical problem. Inspection revealed a partially blocked oil flow path in one of the cooling loops, caused by paper insulation debris restricting oil circulation to that section of the winding.
Outcome
The transformer was taken offline during a planned generation reduction, and the cooling issue was resolved by flushing the affected cooling path. Without the fiber optic monitoring system, this localized heating would likely have remained undetected until significant insulation damage occurred, potentially leading to a major failure. The utility estimated that the early detection prevented a catastrophic failure that would have cost approximately $6.5 million in replacement costs and lost generation.
Key Takeaway
The ability to detect temperature variations between phases and at specific locations within windings enables the identification of cooling problems that conventional monitoring would miss entirely. The temperature differential was well below the absolute alarm thresholds but represented a significant deviation from normal patterns.
Ka Etid 2: Dynamic Loading Capability in Urban Substation Transformer
Background
A major urban utility faced growing load demands in a downtown area served by three 115/13.8kV, 60MVA transformers in a capacity-constrained substation. Load growth projections indicated that capacity would be exceeded during peak summer conditions, but substation expansion was extremely costly and complicated by space limitations and permitting challenges.
Implementation
Rather than immediately pursuing substation expansion, the utility retrofitted the three transformers with fiber optic temperature monitoring systems to enable dynamic loading beyond nameplate ratings when conditions permitted. Each transformer was equipped with 8 fiber optic sensors monitoring winding hotspots, top oil, and ambient conditions.
Operational Strategy
Using the real-time hotspot temperature data, the utility implemented a dynamic loading program that allowed transformers to be safely operated up to 130% of nameplate rating when actual measured temperatures remained below design limits. The system incorporated ambient temperature, cooling system status, and load history into loading decisions.
Results
During the first summer peak season after implementation, the substation successfully handled loads up to 125% of nominal capacity without exceeding design temperature limits. The monitoring system revealed that previous loading restrictions had been overly conservative, as actual winding temperatures remained 15-20°C below critical limits even at these elevated loads. The measured hotspot temperatures showed a strong correlation with ambient temperature and cooling efficiency rather than simply load percentage.
Financial Impact
The dynamic loading capability enabled by the monitoring system deferred a $12M substation expansion project by 4 Ane, while the total investment in monitoring equipment was approximately $425,000. This represented an ROI exceeding 2,000% while maintaining transformer safety and reliability.
Key Takeaway
Real-time fiber optic monitoring enables safe, condition-based loading decisions rather than relying solely on conservative nameplate ratings, unlocking significant latent capacity in existing transformer assets without compromising reliability or asset life.
Ka Etid 3: Early Detection of Developing Winding Deformation
Background
A 400kV/220kV, 500MVA autotransformer in a critical transmission interconnection substation was equipped with 12 fiber optic temperature sensors distributed throughout the windings. The transformer had experienced a through-fault event six months prior but had passed all standard diagnostic tests including DGA, power factor, and short-circuit impedance measurements.
Detection
The fiber optic monitoring system began detecting unusual thermal behavior not evident in conventional monitoring: during daily load cycling, one specific sensor in the common winding showed a thermal response that increasingly lagged behind other sensors in similar positions. While absolute temperature values remained within acceptable limits, the thermal time constant of this specific location had changed significantly compared to baseline data.
Analysis
Advanced analysis of the thermal behavior suggested that the localized change in thermal time constant was consistent with a change in cooling flow patterns potentially caused by minor geometric deformation affecting oil flow channels. This hypothesis was supported by comparing thermal response patterns before and after the through-fault event, showing a clear change in thermal behavior despite normal DGA results.
Verification
Based on the fiber optic data, the utility performed specialized low-voltage impulse (LVI) testing that confirmed subtle winding deformation not detected by standard tests. Subsequent internal inspection during a planned outage revealed minor displacement of winding supports that, while not immediately threatening, would likely have worsened over time with thermal cycling and electromagnetic forces during normal operation.
Outcome
The early detection enabled planned corrective action during a scheduled maintenance window rather than an emergency response to a failure. The utility’s asset management team estimated that recognizing this developing issue early prevented a potential failure that would have cost $8-10 million in equipment damage and replacement, plus untold costs associated with wide-area transmission constraints that would have resulted from an unplanned outage of this critical asset.
Key Takeaway
The detailed temperature data from fiber optic systems can detect subtle changes in transformer thermal behavior that serve as early indicators of developing mechanical problems, even when conventional electrical tests and dissolved gas analysis show normal results.
Common Failure Patterns Detected by Fiber Optic Monitoring
Analysis of numerous case studies reveals several common patterns where fiber optic temperature monitoring has successfully identified developing problems:
Cooling System Degradation
- Signature: Gradual increase in temperature differentials between top and bottom sensors during load cycles
- Early detection advantage: 3-6 months before conventional indicators
- Prevention potential: High – easily correctable if detected early
Localized Winding Distortion
- Signature: Changed thermal time constant in specific winding sections following through-fault events
- Early detection advantage: 6-24 months before electrical test detection
- Prevention potential: Moderate – may require de-tanking but avoids catastrophic failure
Deteriorating Internal Connections
- Signature: Localized heating near lead connections disproportionate to overall loading
- Early detection advantage: 1-3 months before significant damage
- Prevention potential: Very high – relatively simple repair if caught early
Insulation Degradation Hotspots
- Signature: Progressively increasing heating in specific locations even at constant load
- Early detection advantage: 6-18 months before DGA detection
- Prevention potential: Moderate to high depending on location
ROI Analysis: The Business Case for Fiber Optic Temperature Monitoring
The decision to invest in fiber optic temperature monitoring requires clear understanding of both costs and benefits. This section presents a comprehensive business case framework to help asset managers and engineers evaluate the return on investment for different transformer applications.
Implementation Cost Components
Hardware Costs
- Fiber optic temperature probes: $500-$1,500 per sensor
- Signal conditioner/monitor: $5,000-$25,000 depending on channel count
- Extension fibers and accessories: $1,000-$5,000 per transformer
- Installation materials (feedthroughs, junction boxes): $1,500-$3,000
- Communication equipment: $1,000-$3,000
Installation Costs
- Factory installation (new transformers): $5,000-$15,000
- Retrofit installation (existing transformers): $10,000-$30,000
- Engineering design and documentation: $3,000-$8,000
- Commissioning and testing: $2,000-$5,000
Operational Costs
- Annual maintenance and calibration: $500-$1,500
- Software updates and support: $1,000-$3,000 annually
- Data storage and management: $500-$2,000 annually
- Periodic system checks: $500-$1,000 annually
Typical Total Implementation Costs by Transformer Type
- Generation Step-Up Transformer (500MVA+): $50,000-$80,000 for comprehensive system
- Transmission Transformer (100-300MVA): $35,000-$60,000 for standard implementation
- Distribution Transformer (10-50MVA): $20,000-$40,000 for basic monitoring
- Fleet monitoring program (retrofit): $25,000-$40,000 per transformer with shared infrastructure
Quantifiable Benefits
Failure Prevention Value
The primary value driver for most implementations is reducing the probability of catastrophic failures. This value can be calculated as:
Failure Prevention Value = Base Failure Probability × Failure Cost × Risk Reduction Factor
Kote:
- Base Failure Probability: Historical annual failure rate for similar transformers (typically 0.5-2% for power transformers)
- Failure Cost: Total cost of failure including equipment replacement, collateral damage, outage impacts, and environmental cleanup
- Risk Reduction Factor: Estimated reduction in failure probability (typically 30-60% based on industry studies)
Example calculation for GSU transformer:
- Base annual failure probability: 1.2%
- Failure cost: $5,500,000 (including $3M replacement, $1M labor, $1.5M lost generation)
- Risk reduction factor: 50%
- Annual value: 1.2% × $5,500,000 × 50% = $33,000 per year
Extended Asset Life Value
Optimized loading and improved cooling management can extend transformer life beyond design expectations:
Life Extension Value = (Replacement Cost / Original Expected Life) × Years Extended
Kote:
- Replacement Cost: Current cost to replace the transformer
- Original Expected Life: Design life without advanced monitoring (typically 25-40 Ane)
- Years Extended: Additional service years enabled by optimized operation (typically 3-8 Ane)
Example calculation for transmission transformer:
- Replacement cost: $2,800,000
- Original expected life: 35 Ane
- Years extended: 5 Ane
- Annual value: ($2,800,000 / 35) × 5 / 35 = $11,429 per year
Capacity Release Value
Dynamic loading enabled by real-time temperature monitoring often allows safe operation above nameplate ratings:
Capacity Release Value = Capacity Increase × Load Factor × Value of Capacity
Kote:
- Capacity Increase: Additional MVA available beyond nameplate (typically 10-30%)
- Load Factor: Percentage of time that additional capacity would be utilized
- Value of Capacity: Cost of alternative capacity solutions (new transformers, generation, elatriye)
Example calculation for substation transformer:
- Transformer rating: 60MVA
- Capacity increase: 15% (9MVA)
- Load factor for additional capacity: 20% (peak periods only)
- Value of capacity: $50,000 per MVA (based on substation expansion costs)
- Annual value: 9MVA × 20% × $50,000 = $90,000 per year
Maintenance Optimization Value
Condition-based maintenance enabled by detailed temperature monitoring can reduce routine maintenance costs:
Maintenance Savings = Traditional Maintenance Cost × Reduction Percentage
Kote:
- Traditional Maintenance Cost: Annual spending on scheduled maintenance
- Reduction Percentage: Efficiency gained through condition-based approach (typically 15-30%)
Example calculation:
- Traditional annual maintenance cost: $25,000
- Reduction percentage: 20%
- Annual value: $25,000 × 20% = $5,000 per year
ROI Examples by Transformer Class
Transformer Type | Implementation Cost | Annual Benefits | Payback Period | 10-Year ROI |
---|---|---|---|---|
Generation Step-Up (GSU) 500MVA+ | $75,000 | $95,000 (Failure prevention: $65k, Life extension: $15k, Maintenance: $15k) |
0.8 Ane | 1,167% |
Critical Transmission 300MVA | $55,000 | $65,000 (Failure prevention: $40k, Capacity: $20k, Maintenance: $5k) |
0.85 Ane | 1,082% |
Substation Transformer 100MVA | $45,000 | $38,000 (Failure prevention: $18k, Capacity: $15k, Life extension: $5k) |
1.2 Ane | 744% |
Distribution Transformer 25MVA | $30,000 | $16,000 (Failure prevention: $8k, Capacity: $5k, Maintenance: $3k) |
1.9 Ane | 433% |
ROI Calculation Guidance
To develop an accurate ROI analysis for your specific transformer applications, consider these guidelines:
- Prioritize critical assets: Focus initial implementations on transformers where failure would have the highest operational and financial impact.
- Consider fleet-wide efficiencies: Implementing monitoring across multiple similar transformers can reduce per-unit costs through shared infrastructure and volume discounts.
- Evaluate both operational and capital benefits: Include both immediate operational improvements and long-term capital deferral benefits in your analysis.
- Incorporate risk-adjusted values: When calculating failure prevention benefits, use risk-adjusted values that account for both probability and consequence.
- Consider installation timing: Factory installation in new transformers is significantly more cost-effective than retrofits, with better sensor placement options.
- Account for organizational learning: Initial implementations may have longer payback periods as organizations develop expertise in using the data effectively.
Business Case Development Tip
When presenting the business case for fiber optic temperature monitoring to executives or budget committees, emphasize these key points:
- The asymmetrical risk profile of transformer failures (low probability but extremely high consequence)
- The non-linear aging effects of temperature on insulation life
- The value of early detection of developing issues before they become critical failures
- The opportunity cost of constrained transformer capacity in growing load areas
- Case studies from peer utilities that demonstrate real-world value realization
Selection Guide: How to Choose the Right Fiber Optic System for Your Transformers
With multiple fiber optic temperature monitoring technologies and vendors in the market, selecting the optimal solution requires careful consideration of your specific requirements, transformer characteristics, and organizational capabilities. This section provides a structured framework for evaluating and selecting the most appropriate system.
Defining Your Requirements
Before evaluating specific technologies or vendors, clearly define your monitoring objectives and requirements:
Primary Monitoring Objectives
- Failure prevention (focus on reliability)
- Dynamic loading capability (focus on capacity utilization)
- Life extension (focus on aging management)
- Research and development (focus on detailed insights)
- Regulatory compliance (focus on documentation)
Different objectives may lead to different technology choices and implementation approaches.
Transformer Characteristics
- Size and voltage class
- Criticality to system operation
- Age and condition
- Loading patterns (steady, cyclic, emergency)
- Cooling system type (ONAN, ONAF, OFAF, elatriye)
- Replacement lead time and cost
Larger, more critical transformers typically justify more comprehensive monitoring systems.
Installation Constraints
- New manufacture or retrofit
- Access points for retrofit installation
- Available outage windows
- Physical location and environment
- Distance to monitoring equipment
Installation options significantly impact both cost and monitoring effectiveness.
Integration Requirements
- Existing SCADA or DCS systems
- Asset management platforms
- Communication protocols (Modbus, DNP3, IEK 61850)
- Cybersecurity requirements
- Remote access needs
Seamless integration with existing systems increases the value of monitoring data.
Technology Selection Matrix
Based on your defined requirements, use this comparison matrix to identify the most appropriate technology approach:
Requirement | Fluoroptic Point Sensing | Fib Bragg Grating (FBG) | Distribye Sans tanperati (DTS) |
---|---|---|---|
Direct winding hotspot monitoring | Excellent | Good | Fair |
Multiple measurement points needed | Good (up to 16 typical) | Excellent (20+ on single fiber) | Excellent (continuous profile) |
Highest accuracy requirement | Excellent (±0.2 °C) | Good (±0.5 °C) | Fair (±1.0 °C) |
External surface monitoring | Fair (limited points) | Good (multiple points) | Excellent (full coverage) |
Fast dynamic response | Excellent (sub-second) | Good (segond yo) | Fair (minutes) |
Retrofit installation | Good (specialized probes) | Fair (requires special handling) | Excellent (external installation) |
Factory installation | Excellent (robust probes) | Good (requires strain management) | Good (special fibers needed) |
Long-term stability | Excellent (25+ Ane) | Good (strain sensitivity) | Good (requires calibration) |
Fleet-wide implementation | Good (dedicated monitors) | Excellent (multiplexing) | Fair (higher initial cost) |
Budget constraints | Good (scalable) | Fair (higher initial investment) | Poor (highest initial cost) |
Vendor Evaluation Criteria
Once you’ve identified the appropriate technology approach, evaluate potential vendors using these key criteria:
Product Performance
- Accuracy specifications and validation methods
- Temperature range and measurement capability
- Response time and sampling rate
- Calibration requirements and stability
- Communication interfaces and protocols
- Software capabilities and usability
Power Industry Experience
- Years of experience in transformer monitoring
- Installed base and reference customers
- Understanding of transformer thermal behavior
- Experience with your transformer manufacturers
- Case studies and documented successes
- Industry standards compliance (IEEE, IEK)
Installation and Support
- Installation methodology and documentation
- Field service capabilities and coverage
- Training programs for users
- Technical support response time and quality
- Warranty terms and conditions
- Spare parts availability and lead times
Company Stability
- Financial stability and longevity
- R&D investment and product development
- Manufacturing quality control processes
- Industry partnerships and certifications
- Long-term product support commitment
- Merger/acquisition history and stability
Leading Providers in 2025
While a comprehensive vendor evaluation should be performed for your specific requirements, these companies are recognized as leading providers of fiber optic temperature monitoring solutions for power transformers as of 2025:
Qualitrol / Neoptix
Specializing in fluoroptic temperature monitoring systems with extensive transformer installation experience and integration with broader asset monitoring platforms. Their T2 temperature probes have become an industry standard for transformer applications.
Rugged Monitoring
Offers high-accuracy fluoroptic systems with specialized transformer probes and monitoring software. Their systems feature excellent EMI immunity and are designed specifically for harsh electrical environments.
Lumasense Technologies
Provides both fluoroptic and fiber optic distributed temperature sensing systems with a focus on power industry applications, including specialized software for transformer thermal analysis.
AP Sensing
Leaders in high-resolution distributed temperature sensing (DTS) technology with specialized solutions for transformer monitoring, enabling comprehensive thermal mapping with a single fiber installation.
LIOS Technology
Specializes in DTS systems with high spatial resolution suitable for transformer applications, offering solutions that can detect small hotspots along cable runs and transformer surfaces.
Micron Optics / Luna Innovations
Focuses on fiber Bragg grating (FBG) technology for multiple sensing points on a single fiber, with solutions that can monitor both temperature and vibration in transformer applications.
Sensornet
Provides advanced DTS solutions with specialized software for power industry applications, offering high-resolution temperature profiles for transformer monitoring.
Selection Process Recommendations
- Develop detailed specifications based on your monitoring objectives and transformer characteristics
- Issue a targeted RFI/RFQ to qualified vendors with demonstrated transformer experience
- Request detailed reference information from installations similar to your application
- Evaluate total cost of ownership including initial installation, ongoing support, and integration
- Consider arranging site visits to existing installations or requesting demonstration units
- Verify compatibility with your existing systems and data management platforms
- Assess vendor commitment to long-term support and product evolution
Future Trends: The Evolution of Fiber Optic Monitoring in 2025 and Beyond
As we progress through 2025, fiber optic temperature monitoring for transformers continues to evolve, with several emerging trends shaping the future of this technology. Understanding these developments helps utilities and industrial users prepare for next-generation capabilities and ensure that current investments remain future-proof.
Multi-Parameter Fiber Optic Sensing
The most significant evolution in fiber optic monitoring is the integration of multiple sensing parameters beyond temperature in the same fiber optic system:
- Vibration monitoring using the same fibers that measure temperature, enabling detection of mechanical issues including loose windings, core problems, or cooling system anomalies
- Partial discharge detection through specialized acoustic sensing fibers that can pinpoint insulation breakdown locations
- Strain measurement to detect subtle dimensional changes in windings before they cause serious damage
- Moisture content assessment through specialized coating technologies that respond to oil moisture levels
These multi-parameter systems provide more comprehensive transformer health insights while leveraging the same installation infrastructure, improving the cost-benefit ratio significantly.
Advanced Analytics and AI Integration
The value of temperature data is being dramatically enhanced through sophisticated analytics and artificial intelligence:
- Digital twin integration combining real-time temperature data with physics-based transformer models to simulate and predict behavior under various conditions
- Pattern recognition algorithms that identify subtle temperature signatures associated with developing problems
- Anomaly detection using machine learning to establish normal thermal behavior patterns and flag deviations that warrant investigation
- Predictive remaining life models that combine temperature history with insulation aging algorithms to accurately forecast asset lifespan
- Fleet-wide analytics comparing thermal behavior across similar transformers to identify outliers and best practices
These advanced analytics transform raw temperature data into actionable insights that drive maintenance decisions and operational strategies.
Enhanced Integration and Standardization
The integration landscape for fiber optic monitoring is advancing rapidly:
- IEK 61850 profiles specifically for fiber optic temperature data, enabling standardized integration with substation automation systems
- Asset Performance Management (APM) platform integration feeding temperature data into comprehensive health indices and risk models
- OEM integration with transformer manufacturers embedding sensors and offering factory-integrated monitoring solutions
- Cloud-based monitoring platforms enabling centralized analysis of temperature data across entire transformer fleets
- Mobile application interfaces providing field personnel with real-time temperature data and historical trends
These integration capabilities ensure temperature monitoring becomes part of a holistic asset management approach rather than a standalone system.
Technical Performance Advances
Continuous improvement in fiber optic sensing technology is enhancing system capabilities:
- Higher temperature accuracy with new generation sensors achieving ±0.1°C in field conditions
- Enhanced spatial resolution in DTS systems, now achieving 10-25cm resolution for precise hotspot location
- Faster sampling rates enabling real-time transient analysis during fault conditions or switching operations
- Extended operating ranges for extreme environment applications up to 350°C
- Self-calibrating systems with internal reference points ensuring long-term measurement stability
- Miniaturized sensors with diameters under 0.5mm for minimal impact on transformer design
These performance improvements expand the application range and value proposition of fiber optic monitoring.
Economic and Market Evolution
The business landscape for fiber optic monitoring is also evolving rapidly:
- Decreasing system costs as manufacturing scales and component prices decline, making monitoring viable for smaller transformers
- Service-based business models where vendors offer monitoring-as-a-service rather than equipment sales
- Insurance incentives as underwriters recognize the risk reduction value of fiber optic monitoring
- Regulatory recognition of condition monitoring as part of reliability compliance programs
- Industry consolidation as larger monitoring platform providers acquire specialized fiber optic technology companies
These market developments are expanding adoption beyond traditional high-value applications to broader transformer fleets.
Emerging Applications in 2025 and Beyond
Grid-Scale Battery Systems
Fiber optic temperature monitoring is increasingly being adapted for grid-scale battery energy storage systems (BESS) where thermal management is critical for safety and performance. The EMI immunity of fiber optics is particularly valuable in these high-power converter environments.
HVDC Transformer Monitoring
As HVDC transmission expands, specialized fiber optic monitoring systems are being developed for the unique thermal challenges of converter transformers, including the extreme EMI environment and specialized insulation systems.
Phase-Shifting Transformers
Complex phase-shifting transformers with multiple magnetic circuits and windings benefit from comprehensive temperature mapping to optimize performance and identify potential design limitations.
Renewable Integration Transformers
Transformers connected to wind and solar generation face unique thermal challenges due to variable loading and harmonics, driving adoption of advanced monitoring to manage these dynamic conditions.
Strategic Recommendations for Forward-Looking Implementation
To ensure that current fiber optic monitoring investments remain valuable as technology evolves:
- Specify open architecture systems that can integrate with emerging platforms and support multiple communication protocols
- Consider future sensor expansion by installing additional fibers during initial deployment even if not immediately utilized
- Prioritize data accessibility through standard formats and APIs that will support future analytics capabilities
- Select vendors with clear innovation roadmaps who demonstrate commitment to ongoing product development
- Develop internal expertise in temperature data interpretation to maximize value from current and future systems
- Include temperature monitoring in digital transformation initiatives as part of broader grid modernization strategies
- Participate in industry standards development to ensure future interoperability and best practices
Expert Insight: Dr. Elena Michaels, IEEE Transformer Committee
“As we look toward 2030, fiber optic monitoring will evolve from a specialized technology to a standard feature of critical transformers. The integration of temperature data with other parameters like dissolved gas, partial discharge, and vibration will create comprehensive health models that transform maintenance approaches. Utilities implementing fiber optic monitoring today are not just gaining immediate operational benefits but building the foundation for truly condition-based asset management.”
Conclusion: Implementing a Fiber Optic Temperature Monitoring Strategy
Fiber optic temperature monitoring has evolved from an emerging technology to an essential component of modern transformer management. As we’ve explored throughout this guide, these systems offer unprecedented insight into transformer thermal behavior, enabling enhanced reliability, optimized capacity utilization, and extended asset life.
Key Takeaways
Operational Benefits
Direct hotspot measurement provides accurate, real-time visibility into transformer thermal conditions, enabling safe dynamic loading beyond nameplate ratings while preventing dangerous overtemperature conditions. This visibility translates directly into enhanced capacity utilization and operational flexibility.
Financial Value
The business case for fiber optic monitoring is compelling, with typical payback periods under two years for critical transformers. Value drivers include failure prevention, life extension, capacity release, and maintenance optimization, with 10-year ROI often exceeding 500% for important assets.
Technology Evolution
Multiple fiber optic technologies (fluoroptic, FBG, DTS) offer different advantages for specific applications. Technology selection should be driven by monitoring objectives, transformer characteristics, and implementation constraints, with careful consideration of future integration needs.
Implementation Approach
Successful implementation requires careful consideration of sensor placement, installation methodology, system integration, and organizational readiness. Factory installation provides optimal results for new transformers, while several retrofit options exist for existing assets.
Implementation Roadmap
For organizations beginning or expanding their fiber optic monitoring programs, we recommend this implementation approach:
Phase 1: Strategy and Assessment (1-3 Mwa)
- Define monitoring objectives and value drivers
- Conduct transformer fleet criticality assessment
- Identify high-priority candidates for monitoring
- Develop business case and secure funding
- Assess integration requirements with existing systems
Phase 2: Technology Selection (1-2 Mwa)
- Develop detailed monitoring specifications
- Evaluate technology options against requirements
- Issue RFI/RFQ to qualified vendors
- Conduct technical and commercial evaluation
- Select monitoring technology and vendor
Phase 3: Pilot Implementation (3-6 Mwa)
- Implement monitoring on 2-3 priority transformers
- Develop data analysis and response procedures
- Train operations and maintenance personnel
- Establish baseline thermal profiles
- Configure integration with existing systems
Phase 4: Program Expansion (6-24 Mwa)
- Develop fleet-wide implementation plan
- Prioritize transformers based on criticality and opportunity
- Coordinate with maintenance schedules for retrofits
- Specify monitoring for new transformer purchases
- Implement centralized monitoring infrastructure
Phase 5: Value Optimization (Ongoing)
- Develop advanced analytics capabilities
- Integrate temperature data into asset health models
- Implement dynamic loading procedures
- Quantify and report realized benefits
- Continually evaluate new technology developments
Final Thoughts
As transformer fleets age and grid demands evolve, the visibility provided by fiber optic temperature monitoring becomes increasingly valuable. From preventing catastrophic failures to safely extending asset life and releasing latent capacity, these systems offer compelling benefits across operational, financial, and risk management dimensions.
The technology continues to advance rapidly, with enhanced performance, multi-parameter capabilities, and deeper integration with broader asset management platforms. Organizations implementing fiber optic monitoring today are not only addressing immediate operational needs but positioning themselves for the data-driven, condition-based asset management approaches that will define grid operation in the coming decades.
By following the guidelines in this comprehensive guide, utilities and industrial operators can implement effective fiber optic monitoring programs that deliver immediate value while building the foundation for future capabilities. As we navigate the complex challenges of grid transformation and aging infrastructure, these advanced monitoring technologies will be essential tools for ensuring reliability, optimizing investments, and managing critical transformer assets.
Additional Resources
Industry Standards
- IEEE C57.91-2011: Guide for Loading Mineral-Oil-Immersed Transformers
- IEEE C57.118: Guide for Installation of Fiber Optic Sensors in Transformers
- IEK 60076-7: Loading Guide for Oil-Immersed Power Transformers
- CIGRE Technical Brochure 659: Transformer Thermal Monitoring
Technical Papers
- “Transformer Winding Temperature Measurement Using Fiber Optic Technology” – IEEE Transactions on Power Delivery
- “Comparative Analysis of Fluoroptic and FBG Sensors for Transformer Applications” – CIGRE Session Papers
- “Field Experience with Fiber Optic Temperature Monitoring in Power Transformers” – IEEE PES Transactions
- “Dynamic Transformer Rating Based on Direct Winding Temperature Measurement” – EPRI Technical Report
Industry Associations
- IEEE Transformer Committee – Working Group on Fiber Optic Sensors
- CIGRE A2 (Transformers) Working Group on Transformer Monitoring
- Electric Power Research Institute (EPRI) – Transformer Monitoring Program
- International Electrotechnical Commission (IEK) Technical Committee 14
Training Resources
- IEEE Educational Courses on Transformer Monitoring
- EPRI Transformer Health Assessment Workshops
- Vendor-provided Technical Training Programs
- Online Courses on Fiber Optic Sensing Technology
Fib optik Tanperati optik Detèktè, Sistèm siveyans entelijan, Distribye fib manifakti optik nan peyi Lachin
![]() |
![]() |
![]() |